1925.10.15. Wittenberger Zeitung
Wanderung durch die Betriebe der Wittenberger Industrie
Kalkstickstoff wird bei uns in größerem Ausmaße erst seit einigen Jahren hergestellt, so daß die nähere Schilderung Walter Fischers in der „Technik für Alle“, der wir folgendes entnehmen, wohl vielen Neues bringen wird.
Die Bedeutung des Kalkstickstoffs für die Landwirtschaft liegt besonders darin, daß er im Gegensatz zu den Kalisalzen und dem Ammonsulfat keine Säure in den Boden bringt, sondern im Gegenteil basischen Kalk zuführt. Da aber eine zuweitgehende Versäuerung des Bodens nachteilig ist, mithin der Steigerung der Düngerzugabe Grenzen gesetzt sind, ist diese Gefahr für den Kalkstickstoff nicht vorhanden.
Eine Starkstromleitung führt vom benachbarten Großkraftwerk Zschornewitz-Golpa elektrische Energie als 80 000 Volt Dreiphasendrehstrom dem ersten Gebäudekomplex zu. Vier riesige Transformatoren mit Oelkühlung, lange Zeit die größten in ganz Deutschland, spannen den Strom zunächst auf 6000 Volt um. Auf breiten, bunt markierten Schienen wird die Elektrizität weiteren Umformern zugeführt, in denen sie auf die benötigten Betriebsspannungen herabgesetzt wird. Ein blitzsauberer Schaltraum regelt die Stromverteilung auf die einzelnen Gebäude. Rote, grüne, weiße Glühlampen auf den blinkenden Schalttafeln geben genau Auskunft, über den weiteren Weg der Energie; automatische Schreibinstrumente ermöglichen eine genaue Betriebskontrolle von dieser Zentrale aus; Feuermeldeanlagen zeigen selbsttätig den Ausbruch eines Brandes an. Im gleichen Block sind auch die Pumpen aufgestellt, die das im Werk benötigte Wasser (gegen 5000 m3 stündlich ) aus der Elbe in die Sammelbehälter heben.
Dröhnen und Donnern empfängt uns beim Betreten des nächsten Gebäudes. Es sind die Mühlen, die den gebrannten Kalk und Koks zerkleinern. Diese einheimischen Produkte wandern sodann in die runden, etwa 3 Meter im Durchmesser großen Karbidöfen. An gewaltige Ketten hängende Kohleelektroden, die vom Führerstand genau reguliert werden können, vermitteln die Stromzuführung. Die Elektrizität erzeugt beim Durchgang durch das Kalk-Koksgemisch nach der als Gegenelektrode wirkenden, aus Kohle bestehenden Bodenplatte eine Temperatur von rund 3000° C. Dabei vereinigt sich Kalzium mit Kohlenstoff zu Kalziumkarbid, während das dabei entstehende Kohlenoxyd hellbrennend nach oben abzieht. Riesige Staubwolken geben Kunde von der Gewalt dieser Reaktionen. Neuerdings geht man dazu über, die Oefen abzudecken, um das Kohlenoxyd zu gewinnen und für das Brennen des Kalksteins nutzbar zu machen. Die dadurch erreichbare Brennstoffersparnis ist recht ansehnlich. Wenn man heute den geregelten Betrieb sieht, ahnt man kaum, welche Erfahrungen erst gesammelt werden mußten, um so weit zu kommen. Gehörten doch Explosionen infolge zu feinen Korn der Beschickung im Anfang zu den häufigen Erscheinungen, bis man endlich die passende Korngröße gefunden hatte.
Steigt man von der Beschickungsplattform hinab, so sieht man ein seltsames Schauspiel: Hinter einem fahrbaren Eisenschild rücken mehrere Leute der Ofenwand mit einem mittelalterlich, anmutenden Sturmbock zu Leibe. Aber es ist eine recht moderne Maschine: der vermeintliche Mauerwidder ist eine kräftige Kohleelektrode, mit der man die äußere, harte Karbidschicht des Ofens durchschmilzt, bis in hellem Strome, das Auge blendend, das weißglühende Karbid hervorbricht. Mit eisernen Stangen hält man den Ausfluß offen, während ein eiserner Wagen nach dem andern sich mit der heißen Masse füllt.
In einer weiten Halle werden die Kästen der Karren auf Böcken abgesetzt, um auszukühlen. Gewaltige Wärmemengen gehen hier nutzlos verloren. Das erkaltete Karbid nimmt begierig die Luftfeuchtigkeit auf und entwickelt Azetylen, wie man am Geruche merkt. Aber dieser Zersetzung läßt man keine Zeit. Die Karbidblöcke werden sofort in starken Backenbrechern zerkleinert und in Rohrmühlen zu feinem Pulver zermahlen. Das feine Mehl wird in mit Wellpappe ausgekleidete, durchlochte Blechzylinder eingetragen und dann in eiserne, sogenannte „Azotiergefäße“ eingelassen, in denen das Kalziumkarbid im gasförmigen Stickstoff zu Kalkstickstoff (Ca CN2) umgesetzt wird. Diese Reaktion erfolgt unter Wärmeentwicklung, beginnt aber erst bei 900-1000° C. Um diese Anfangstemperatur zu erreichen, stößt man in das Karbidmehl ein Papprohr und setzt in dieses einen dünnen Kohlestab. Dann verschraubt man den Deckel des Gefäßes, läßt von unten her Stickstoff eintreten und bringt durch Kontaktschluß den Kohlestab zum Glühen. Ist die Reaktion dann eingeleitet, so genügt die Umsetzungswärme zur Fortführung das Ende des Prozesses erkennt man am Manometer. Dann hebt man den inneren Zylinder mittels Laufkrans heraus und bringt den Kalkstickstoff, eine dunkelgraue gesinterte Masse, die noch Kohlenstoff Aetzkalk und etwas unzersetztes Karbid enthält, zu den Mühlen. Das Mehl wird schließlich noch mit Teeröl versetzt, um das Stauben zu verhüten, und in Säcken als Düngemittel zum Versand gebracht. Seine vorzügliche Wirkung beruht auf einem Gehalt von 20 Prozent Stickstoff und 60 Prozent Kalk.
Dieses Verfahren, daß von den Professoren Frank und Care ausgearbeitet worden ist, benötig, wie wir sehen, reinen gasförmigen Stickstoff. Zur Gewinnung desselben sind zwei Verfahren in Anwendung:
1. Man verflüssigt Luft in Lindemaschinen und fraktioniert anschließend, wobei zuerst reiner Stickstoff verdampft, während flüssiger Sauerstoff übrigbleibt und anderweit verwendet wird.
2. Man verbrennt Generatorgas , wobei Kohlensäure, Kohlenoxyd und Stickstoff sowie etwas Sauerstoff übrigbleiben. Dieses Gasgemisch leitet man über Kupferoxyd; dabei wird das Kohlenoxyd zu Kohlensäure oxydiert und metallisches Kupfer gebildet, welches den Sauerstoff an sich reißt und wieder Kupferoxyd bildet. Die entstandene Kohlensäure wird unter 22 Atmosphären Druck in Wasser gelöst und der verbleibende reine Stickstoff für die Azotierung des Karbids verwandt. Die gelöste Kohlensäure wird später ausgetrieben und die Druckdifferenz zum Antrieb von Gasturbinen ausgenützt.
Der Kalkstickstoff dient nun nicht nur als Düngemittel, sondern bildete besonders im Kriege ein wichtiges Ausgangsprodukt für die Darstellung von Salpetersäure. Um zu dieses zu gelangen, ist zunächst eine Zersetzung des Kalkstoffes zu Ammoniak nötig. Dazu wird es als feines Pulver in mehrere Etagen hohe Druckzylinder, sog. Autoklaven, eingetragen, und durch Dampf von etwa 170 ° C in kohlensauren Kalk und Ammoniak zerlegt. Niesreiz und brennende Augen zeigen diese Reaktion auch dem Nichtchemiker an. Der abfallende Kalkschlamm wird zurzeit als Düngemittel verwandt, während das Ammoniakwasser früher zum Teil der Salpetersäurefabrik zu geführt wurde. Jetzt, wo der Kalkstickstoff so begehrt ist, verwendet man in Piesteritz vornehmlich Ammoniakwasser aus den Leunawerken und einigen Gasanstalten hierzu.
Zu diesem Zweck treibt man aus dem Gaswasser in hohen Kolonen das Ammoniak aus, versetzt es mit ungefähr dem dreizehnfachen Volumen Luft und leitet es in die von Frank und Caro konstruierten Oxydationsöfen, Aluminiumapparaturen, in denen das Gasgemisch ein durch Elektrizität auf Rotglut erhitztes feinmaschiges Platinnetz passieren muß. Dabei entstehen Wasserdampf und Stickoxyde, besonders Salpetersäureanhydrid. In hohen Rieseltürmen aus Granit und Steinzeug bildet das Anhydrid mit Wasser dann Salpetersäure. Pumpen und Kühler aus säurefestem Kruppschen Spezialstahl dienen zur Bewegung und Kühlung der abfallenden, etwa 65 prozentigen Säure, die entweder direkt zum Versand gelangt oder auf Salpeter bzw. das explosible Ammoniumnitrat verarbeitet wird. In jüngster Zeit ist außerdem die Darstellung von Cynnatrium aufgenommen worden.
So zeigt das Piesteritzer Werk besonders schön die vielseitige Verwendbarkeit einfacher, einheimischer Rohstoffe, wie sie durch die Arbeiten deutscher Forscher ermöglicht worden ist. Deutschland ist dadurch instand gesetzt worden, sich von der Einfuhr des Chilesalpeters freizumachen, und hat dabei noch den Vorteil, daß die Stickstoffdünger heute billiger sind als vor dem Kriege.
aus: Brockhaus 1924
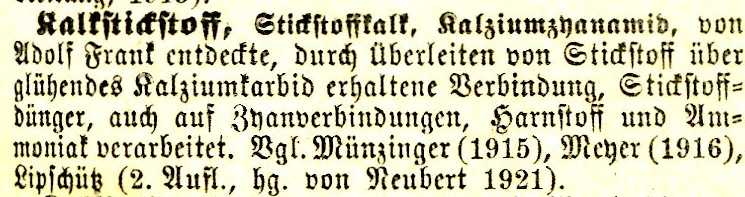