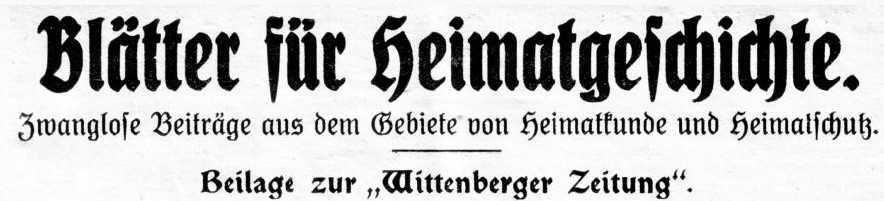
Die Bedeutung des Namens Wittenberg habe ich leider bisher nicht ergründen können, das Bild unseres Stadtwappens gibt darüber keinen Aufschluß, ein Geschichtswert, das sich mit den Uranfängen unserer Stadt beschäftigt, existiert noch nicht. Allzuhoch wird man das Alter der Stadt nicht schätzen können, denn sie ist zuerst urkundlich im Jahre 1180 erwähnt worden. Vor altersgrauer Zeit, als die Stelle, auf der die Stadt und Umgebung heute steht, noch unbesiedelt war, mögen die hier an die flachen Elbufer herantretenden Höhen weiße Sandberge gewesen sein, und dieser Anblick mag dem vorüberfahrenden Schiffer, dem ersten Kulturpionier, Veranlassung gegeben haben, diese Stelle die witten, d.h. weißen Berge zu nennen. Sand genug hat die Umgegend von Wittenberg, leider; den Besitzern der Felder wäre es gewiß lieber, wenn hier Weizen und Rüben wachsen wollten. Aber der liebe Herrgott hat es einmal anders eingerichtet, und hat dafür gesorgt, daß die „witten Sandberge“ schließlich doch auch wieder manche wertvollen Bestandteile in sich enthalten, die den Menschen zu seinen Bedürfnissen allmählich zu nützlichen Erfindungen verholfen haben.
So ist den Einwohnern von Dobien und Umgegend schon lange bekannt gewesen, daß sich in den welligen Sandbergen um ihren Ort herum und auch bei den Orten Nudersdorf und Braunsdorf mehr oder minder tiefe, vereinzelt gelagerte Rippen von wertvollem Ton befinden, dessen Gewinnung und Aufbereitung zu einer bemerkenswerten keramischen Industrie geführt hat.
Hart südlich Dobien, dort wo die Chaussee die ersten höheren Sandwellen überquert, hat sich im Jahre 1918 das Tonwerk angesiedelt und aus kleinen Anfängen zu stattlicher Größe entwickelt, das trotz der Ungunst der Lage zu einer größeren Bahnstrecke und der damit bedingten Verteuerung des Bezuges von Brennwerk sich dennoch tapfer weiter entwickelt hat und jetzt als durchaus gesichertes Unternehmen dasteht.
Das Tonwerk ist wirtschaftlich hervorgegangen aus dem früheren Zastrow – Werk, das in der Nähe des Lutherbrunnens eine Ziegelei und ein Majolikawerk betrieb(bei Majolika handelt es sich um Keramik oder Steingut, das mit einer weißen Zinnglasur überzogen ist und anschließend mit Farben bemalt ist).
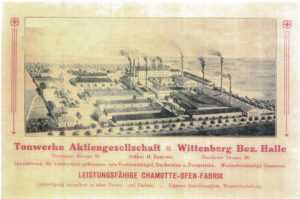
Dresdener Straße 50 (früher Zastrow)
aus: Archiv des HV WB
Letzteres brannte ab und ist nicht wieder aufgebaut worden; und der Ziegeleibetrieb mußte eingestellt werden, weil in der nächsten Umgebung die Tonausbeutung aus den Sandbergen versagte und die Heranschaffung des Tons aus den Elbwiesen sich als zu kostspielig und unrentabel erwies. Nachdem man in den Sandbergen von Dobien, vielfach allerdings schon auf Teucheler Flur durch systematische Bohrungen Tonvorkommen in ausgedehnten Rippen festgestellt hatte, die von guter Beschaffenheit lohnende Verwertung versprachen, ging man dazu über, das alte Zastrow – Werk in der Nähe des Lutherbrunnens abzubrechen und bei Dobien wieder zu errichten.
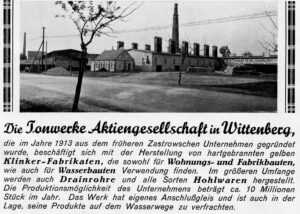
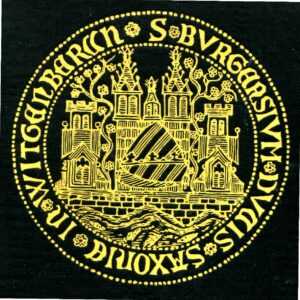
Dort liegt es nun auf Wittenberger Flur wie auf einer Insel, während die Felder rings herum schon zu anderen Nachbarorten gehören. Das Tonwerk hat sich seit 1918 durch An- und Neubauten sowie Verbesserungen aller Art, ständig vergrößert, stellt ein vorzügliches Material her und hat sich dadurch einen festen Abnehmerkreis gesichert, der es ihm ermöglicht hat, den Betrieb über die augenblickliche Geschäftsstille auf dem Baumarkt wie auf allen Gebieten des Handels und Verkehrs soweit hinüberzuretten, daß er nicht stillgelegt zu werden brauchte. Er konnte, wenn auch nicht immer in vollen Schichten, aber doch ohne Unterbrechung dank der äußerst fachgemäßen kaufmännischen und technischen Leitung in Gang gesetzt werden.
Um die langfristige Sicherung der Gewinnung des wertvollen Tons aus den umliegenden Sandfeldern hat das Tonwerk mit den Besitzern der angrenzenden Ländereien langfristige Pachtverträge abgeschlossen, die es ihm ermöglichte unter ganz bestimmten Gesichtspunkten die Tonrippen abzubauen, und um dies näher in Augenschein zu nehmen nehmen, müssen wir uns auf die sandigen Höhen, von denen man übrigens einen prachtvollen Rundblick auf eine ganze Reihe der nächsten Ortschaften hat, hinausbegeben.
Vom Werk führt eine Schmalspurbahn, die von einer etwa 50 pferdigen Lokomotive mit kleinen Kippwagen befahren wird , hinaus zu den Tonschächten. Diese liegen mehr oder minder tief unter dem Sande und weisen zu nächst oben eine dunklere, magere Schicht, weiter in der Tiefe den helleren, sogenannten blauen, fetteren Ton, das Hauptmaterial auf, das eine ziemliche Zähigkeit besitzt; denn um ihn mit Vorteil von Ort bewegen zu können, muß er nach Anbohrung gesprengt werden, damit er mit den zerfallenen Stücken leichter verladen werden kann. Ein gut wirkender Sprengschuß löst mindestens soviel Trümmer ab, wie zwei Kippwagen aufnehmen können. Durch Sprengen und Ausschaufeln bringt man in die Rippen eine vertiefte Bahn hinein, auf der dann wieder Gleis verlegt werden kann, so daß nunmehr die Arbeiter von beiden Seiten die Wagen befüllen und bequemer hantieren können.
Die ausgehobenen Massen werden nun mit der Kleinbahn auf eine Halde dicht bei der Fabrik gebracht und dort nach jahrelanger Erfahrung in gewisser Mischung übereinander abgeladen und zwar der blaue Ton in der Hauptsache, daneben der dunklere Ton zur Färbung und Magerung, dazwischen etwas Sand usw. Das Ganze wird häufig gewässert und bleibt ungefähr ein Vierteljahr liegen, damit es zu einer homogenen Masse zusammensintert, wie sie das Fabrikat nun einmal erfahrungsgemäß erfordert. Dieser Tonberg, der horizontal aufgeschichtet wurde, wird nun wie mit Spitzhacken vertikal abgebaut, um die ungleichartigen Bestandteile weiter gleichmäßig zu verteilen und mittels Förderwagen in die Fabrik gezogen, wo ein Zubringer das Gemenge automatisch in den Kollergang abgibt. In diesem laufen zwei schwere aufrecht gestellte Mahlsteine mit nachfolgenden Kratzeisen auf einer kräftig durchlochten Platte umher, zerreiben die Tonmassen und mischen sie nochmals innig miteinander und drücken sie durch die Löcher der Bodenplatte hindurch. Ein Förderband nimmt die wurstförmigen Preßstücke hoch und schüttet sie auf ein ungleichmäßig laufendes Walzenpaar, das sie wiederum zerreißt und zu feinem Brei verarbeitet, der nun schon eine ziemlich gleichartige Zusammensetzung zeigt. Eine Förderschnecke preßt den Brei durch eine Form, und aus dieser kommt nun der Stein als langes Band zum Vorschein, um alsbald mit einer Drahtschneide zu einzelnen Steinen zerteilt zu werden. Die noch stark feuchten Steine, die ungefähr 1 Kilogramm Wasser enthalten, müssen bei der Pressung und Formung ein solches Ausmaß erhalten, daß sie nach vollendeter Trocknung und bewirktem Brennen die sich immer gleichbleibenden, in ganz Deutschland als Norm festgelegten Maße von 25 mal 12 mal 6,5 Zentimeter bekommen. Frisch aus der Presse genommen, hat der nasse Stein deshalb z.B. in der Länge etwa 2 Zentimeter, also 27 Zentimeter. Sobald der Stein hinter der Presse abgeschnitten ist, wird er auf eine Förderbahn gehoben, und diese führt ihn an endloser Kette zu den Trockenräumen.
Diese bestehen entweder aus offenen Schuppen mit Holzgestellen und Auflagebrettern oder in Trockenhorden über dem Ringofen. Auf diesen wird im Winter und bei feuchter Luft, in offenen Schuppen im Sommer getrocknet. Die großen Trockenschuppen können 160 000 Steine bergen und ebenso viele Steine faßt der Ringofen bei voller Beschickung So ein Ringofen ist eine im Grunde genommen sehr einfache, aber doch wiederum sehr sinnreich ausgedachte und nur auf Grund jahrzehntelanger Erfahrung zur jetzigen Vollendung gebrachte Einrichtung, um durch das eigentliche Brennen der Steine mit der abströmenden Hitze zugleich die Steine der nächstfolgenden Kammern vorzuwärmen, weiter zu trocknen und so allmählich für den eigentlichen Brennprozeß vorzubereiten.
Die Arbeitsweise im Ringofen geht folgendermaßen vor sich: Der Ringofen besteht aus 18 Kammern, und das Feuern und Herausnehmen sowie das Wiedervollpacken der Steine geschieht ungefähr diametral gegenüber in dem länglich – runden Ofen. Wenn also z.B. in der Kammer Nr . 1 gefeuert wird, hat sich Nr. 8 inzwischen soweit abgekühlt, daß sie ausgepackt werden kann, während Nr. 9 leer steht und Nr. 10 wieder voll gesetzt wird. Das eigentliche Befeuern geschieht durch Zuschütten von Braunkohle durch röhrenartige Schächte von oben in die bereits zu einer gewissen Glut vorgewärmte Kammer, die ihre Hitze aus der daneben liegenden erhalten hatte. Durch das Beschicken mit Kohle wird die höchste Hitze von ungefähr 1200 Grad erzielt, bei welcher der Stein in ungefähr 1,5 Tagen fertig gebrannt wird. Ist diese Kaminer fertig, so wird die nächste bereits auf 900 Grad gebrachte Kammer mit Braunkohle beschickt usw. Beim Einsetzen der frischen Steine in eine Kammer wird diese gegen die Vorkammer mit Papier abgesperrt, um das Nachströmen kalter Luft zu verhindern. Diese Papierwand geht später, wenn die von Kammer zu Kammer stärker werdende Hitze sie erreicht hat, von selbst in Flammen auf und gestattet nunmehr der immer höher steigenden Wärme den vollen Zutritt. Dieses bewirkt man für die einzelne Kammer nacheinander durch Ziehen einer Glocke, deren Gestänge durch die Decke des Ofens nach oben hindurchreicht und von dort bedient werden kann. Der Ringofen faßt in seinen sämtlichen 18 Kammern zusammen genommen 160 000 Steine und diese können bei regelmäßigem Gange in zehn Tagen fertig gebrannt sein.
Das Werk erzeugt im Jahre gegen 8 Millionen Steine bzw. andere Gebilde in Form von Röhren, Hohlsteinen, Formsteinen usw., diese letzteren aber auf Mauersteine in obiger Zahl umgerechnet.
Der nasse Stein, wie er die Ziegelpresse verläßt, sieht dunkelgrau, ins bläuliche schimmernd, aus, der fertige Stein hat durch das Trocknen und Brennen eine schöne gelbe, leuchtende Farbe angenommen, die sich vorzüglich für Fassaden besserer Gebäude eignet und einem kunstverständigen Architekten ein großes Feld der Verwendung nach Schönheits- und Festigkeitsmomenten freigibt.
Neben den Normal – Ziegelsteinen werden Lochsteine zur Hintermauerung und für Zwischenwände, Hohlsteine mit besonderem Profil für Decken, ferner Röhren der verschiedensten Kaliber hergestellt.
Ein Anschlußgleis der Wittenberg – Straacher Nebenbahn führt bis auf den Werkshof und bringt die Braunkohle heran, die von besonderer Art sein muß, um die an sie gestellten Ansprüche für eine gute Befeuerung der Kammern zu befriedigen. Ein Teil dieses Anschlußgleises durchzieht den Werkshof vertieft, so daß die Fertigware wie zu ebener Erde bequem in die Wagen verladen werden kann. Das Werk beschäftigt ungefähr 300 Arbeiter und Angestellte, erstere zumeist aus den umliegenden ländlichen Ortschaften, womit den Ansässigen auf den leichten, wenig ertragreichen Sandböden der nächsten Umgebung lohnender und sicherer Verdienst zugewendet wird, der um so mehr zu begrüßen ist, als diese Leute sonst womöglich zur Auswanderung gezwungen wären, und dann dem deutschen Vaterlande erfahrungsmäßig zum größten Teil für immer verloren gehen.
***
aus: Wittenberger Zeitung vom 21.04.1926.